![]() | ![]() |
---|---|
![]() |
HOMOGENIZING PUMPS
Homogenizing – the subdividing of particles into smaller particle sizes creating a stable solution ideal for further processing.
CALL NOW!
016 455 1460/1
HOMOGENIZING THEORY
The un-homogenized product enters the first stage of the valve chamber at high pressure and low velocity. Homogenizing occurs when the product enters the adjustable, close clearance area between the valve and the valve seat. At this stage there is a rapid increase in velocity with a corresponding decrease in pressure, resulting in an intense energy release, localized pressure differences and turbulence rupturing the particles. The homogenized product having impinged on the impact ring exists the valve chamber at a pressure sufficient to transport it to the next stage in the process. A single stage valve assembly is usually preferred for the processing of dispersions or emulsions, whereas a second stage would improve the stability of most emulsions. If narrow particle size distribution is required it may be necessary to introduce two or more homogenizing stages. This can be achieved by recirculation the product through a single stage, or using two or more homogenizers in serie
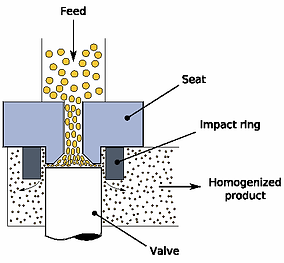
WHAT TO CONSIDER WHEN PURCHASING A HOMOGENIZER
There is one more factor to remember when buying homogenizing units, which are sometimes equally as important as pressure and flow rate. That's work. The kind of work that the clientele expects the Homogenizing Pump needs to do.
WORK:
The unit for pressure is measured in bar, which actually determines how much pressure is required. Our models typically have a pressure range from fifty (50) bar pressure up to one thousand six hundred (1600) bar pressure. The degree of homogenization is a function of the difference between the pressure of the emulsion at the inlet of the valve and the pressure at the outlet of the valve.
PRESSURE RANGE (BAR):
The unit of product flow/emulsion is cubic meters per hour, which is actually the amount/quantity of product/emulsion produced in a one hour period. For a constant flow rate pump, a desired homogenizing pressure is maintained by adjusting the gap between the valve member and the valve seat.
FLOW:
This parameter refers to the volume, or sample size, to be homogenized. It is possible that multiple sample sizes, from microliters to thousands of litres, can be processed using the same homogenizer unit. However, you will need to purchase the appropriate accessories, probe, or tool to match the volume range.
PROCESSING RANGE (ML):
Speed control is a common feature on multiple types of homogenizers. For mechanical homogenizers, “it is best to start off slow and gradually increase speed, (and) make sure you are in control at all times. If precise control is needed then you might want to consider a unit that provides an optional external speed control box.
SPEED CONTROL AND RANGE (RPM):
MOTOR SIZE (WATTS):
The requirements of the motor size, generally measured in power or Watts, are application specific.
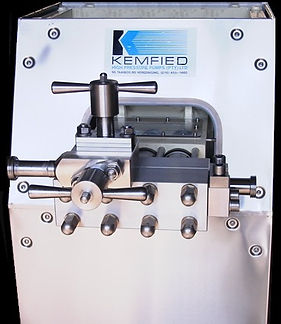
Once the homogenizer has been sized/specified in relation to the kind of work to be performed (processes), choosing the right homogenizer/manufacturer is critical.To aid our clientele with their homogenizer requirements, the below implications are to be considered:
-
Ease of maintenance.
-
Speed of change over.
-
Up Time.
-
Cost Effectiveness
-
Spares Availability
-
Technical Support and Back Up
-
Product Quality
-
Consistency and Reliability
MANUFACTURER/SUPPLIER?
WHY PURCHASE A KEMFIED HOMOGENIZER?
By evaluating and considering additional technical needs and requirements, our homogenizing pump/unit allows independent adjustment of flow rate and shearing rate, allowing direct control of the particle and droplet size, as well as the particle and droplet distribution
Manufacturing our components, valve/pump/unit (homogenizer), to:
-
treats your products gently
-
be as economical with resources as possible
-
meet high demands on flexibility – by way of your current and future production
-
requirements
-
be a long term cost effective investment
-
reduced process time
-
rationalized the production processe
-
liminate cross contamination
-
reduced energy consumption - through equipment and high efficiency motors/drives - through efficient pipe and tank insulation - through efficient heating and cooling transfer systems
-
increased yield through product recovery
-
reduce noise emission
-
be ergonomically compliant
-
meet safety standards
-
the highest quality standards
KEMFIED HOMOGENIZERS
KEMFIED designs employ the most advanced technology in high pressure Homogenizing and reciprocating piston pumps. Manufactured exclusively in accordance with our customer process requirements.
Thus our HOMOGENIZERS do not only convince with extraordinary quality and reliability, but also provide huge benefits in other important areas.
-
The Homogeniser is the machine which is most subjected to stress in the production line.
-
The parts involved in the transmission possess the mechanical sturdiness necessary for the performance required.
It is safe to use and is easy to install, operate and maintain
FRAME
The frame has been designed to optimise internal hygiene of the machine, sturdily built, allowing ease of access. The standard cladding being satin-finish stainless steel (304)2B or alternatively to customer specific requirements.
RECIPROCATING PISTON PUMP
Kemfied pumps are known worldwide for high quality, high pressure plunger pumps manufactured in South Africa applying German technology. The manufacturing of Kemfied high pressure pumps is done through constant research and development by our research and development department which brings new ideas and products to the world market. Kemfied pumps are rated from 0 – 2500 bar working pressure, complying with South African standards of quality and reliability (SABS). Our pumps have applications for industry in general such as- petrol chemical plants, heat exchangers, ship cleaning, removing touch down rubber from airport runways, concrete cutting and demolishing, underwater cleaning, domestic uses, HOMOGENIZERS and many other applications.

CHARACTERISTICS:
-
Ease of Maintenance
-
Reliability - A unique method of fixing the pump plunger ensures perfect alignment through its water lubricated guides and seals leading to excellent seal life.
-
Compact - Lightweight either fixed mounted or trailer mounted for ease of mobility
-
Safety - water pressure sensing throttle control monitors operator demand and adjusts output
-
Cost Effective – Kemfied locally manufacture own spare parts thus clientele save money and have more uptime.
PUMP FEATURES:
-
Built-in Gearbox
-
Double Centre five (5) Bearing Crank Support,(prevent cracking or possible breakage)
-
Force Feed Oil Lubrication,
-
Integrated Oil Cooling System (optional)
-
Water Cooled Crank Casing,
-
Self Aligning, Water Cooled, Tungsten Coated Plungers,
-
Fluid End - Safety Valve
-
Glycerin filled pressure Gauge

PLUNGERS
Depending on homogenizing process system required plungers are manufactured using ceramic materials alternatively Tungsten coated which enables the incorporation of highly abrasive resistant and durable components. Plungers are allocated within each pump head which can contain different diameter to control machine capacity at reduced cost.The motion of the plungers, are guided by special guide rings and swivel, allowing the plungers to self aligning This means that the seals of the plungers are spared this task, thus assuring a longer working life.
FLUID END
The “Fluid End” is the machine part by which the product is pumped at high pressures pump into the valve chamber.
This part is critical on all homogenizers because subject to pulsating fatigue stress due to pumping action of the machine.
We have combined the specific know-how in materials selection, manufacturing technology and fluid-dynamics analysis, using technological core competences acquired in all the years of experience to design our “Fluid Ends” featuring an ultra clean configuration suitable for clientele application, to the compression block according to the machine working pressure.
We have based our pump “Fluid End” manufacturing and design on a smooth internal block profile without dead ends and recesses, minimizing stress concentration:
-
removable Valve Seats,
-
interchangeable Ball and Poppet pump Valve configurations, Relief/Safety Valve -specially designed so that if the primary regulating device fails to by-pass at a set system pressure, the relief valve will open and allow liquid to flow freely.
-
A relief valve can save costly pump and system damage, and more importantly it’s an added safety feature to protect those working around the equipment.
-
equipped with Rupture Disc so should and only if the primary regulating device fails (human error) to by-pass at a set system pressure or a blockage, the disc shall “rupture” stopping the pump and homogenizing system immediately avoiding any damage to emulsion and equipment.
The Homogenizing Valve (The Heart Of Any Homogenizing Pump)
In order to permanently mix one or more substances in a liquid, a homogenizer must be used that makes it possible to micronize and disperse the suspended particles in the fluid, rendering it highly stable even during successive treatments and storage. Thus the most critical component of the homogenizing system is the valve technology. Kemfied has established itself as the leader in developing a wide range of technologically advanced valves for a wide range of applications. Our engineers are committed to working with you every step of the way to ensure the homogenizing valve configuration and material selection are customized for your specific application. The two/double-stage valve assembly is recommended for most emulsions.

Single-stage assembly is preferred for most dispersion.

No matter what your application is, we have the solution that will optimize performance for your specific processing conditions.
CONTAMINATION
We have constructed the components in the Kemfied homogenizing system with high strength, non-shedding materials so that no unwanted matter contaminates the emulsion product, although thorough cleaning as to any equipment is required in general and especially should our client alter emulsion product.
CLEANING
Depending on product and containment requirements, cleaning may be done by flushing or circulating solutions such as hot or cold water or chemical cleaning solutions at little or no pressure. Water at temperatures up to ninety three degree Celsius (93°C) may be circulated without damage to seals or packing. For higher temperatures such as steam cleaning, other packing and seal materials may be required. Chemical solutions containing acids, caustic bases or halides (chlorine, bromine, iodine, etc.) must be flushed and neutralized and not allowed to remain in the pump.
If properly cared for and regularly maintained, the investment you make today can last for decades.

96 Taaibos Road, Powerville
Geo: -26.686353, 27.911795
P. O. Box 1850, Vereeniging, 1930
Gauteng, 1930, South Africa
Tel: 016 455 1460 Fax: 016 421 2824
Email: technical ingo@kemfied.co.za Accounts info@kemfied.co.za